Study and Analysis of a Root Cause of Failure
in Resin Composite Materials
Analysis of Failure and Damage of Plastics and Rubbers
JFE-TEC is ready for identifying the root cause of failure with molded products of plastics and rubbers and solving it.
Molded products of plastics and rubbers fail with different reasons.
Analysis of the root cause of the failure is critical for improvement of the product quality and accelerates the activity in research and development of molded products.
The cause of molded parts failure is derived from the production process and from the usage in different environment.
- Root cause of the failure related to the production process Problems in blending of raw materials and in molding processes (improper molding condition, poor drying of raw materials, and contamination with foreign particles)
- Root cause of the failure related to the usage environment Degradation of molded parts is divided into degradation caused by the chemical reactions such as ultraviolet degradation, thermal oxidative degradation, hydrolysis degradation, and chemical exposure degradation and degradation caused by physical effects such as creep, vibration, and heat.
Investigation of cause of failure and analysis subjects
-
Morphology analysis of crack surface and fracture surface
Fractography by the scanning electron microscopy (SEM) and the optical detection method with a high resolution charge coupled device CCD camera allows the analysis of the crack initiation, crack propagation, and the mechanism of crack formation. - Non-destructive analysis by the transmission electron microscopy can identify the presence of weld-line and voids in molded parts.
- Analysis of morphology of the filled materials in the composite resins can determine the degree of orientation and dispersion of filled materials such as glass fiber, inorganic fillers, and rubbers.
Failure example of molding forming and materials
-
(1)Severe molding condition and poor flow of resins
Photo Cracking at the gate location -
(2)Loss of mechanical strength caused by poor adhesion between glass fiber and resin
Photo Electron micrograph of the fracture surface
Example of cracking under use environment
(1)Root cause of the failure: Creep rupture (ductile failure).
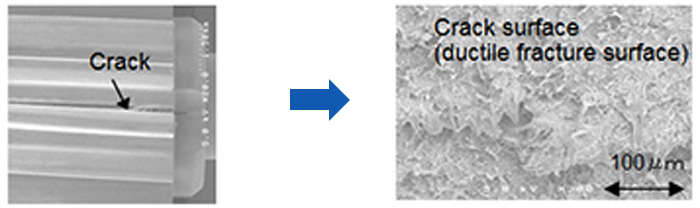
(2)Root cause of the failure: Solvent crack by exposure to ester-type oils
-
Photo Electron micrograph of the surface of
cracked molded parts -
Photo Electron micrograph of the crack surface
of molded parts
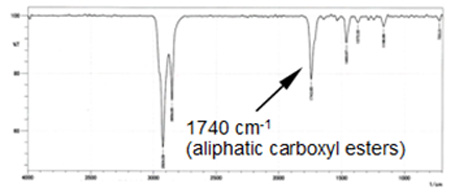
Material fracture modes estimated from fracture surface
-
(1)Ductile fracture
suggested by the formation
of dimple patterns -
(2) Brittle fracture by
exposure to the chemical
from Chevron*1 pattern
whose company logo is left
on the surface.*1 Company's logo -
(3) Fatigue failure suggested
by the spacing of fatigue
striations*2*2 Regular spacing of the stripes matching to the successive stress cycle.
Failure solution example by fractography
An analysis example in which a change of the raw materials caused loss of the mechanical strength of molded parts (material: glass fiber reinforced plastic)
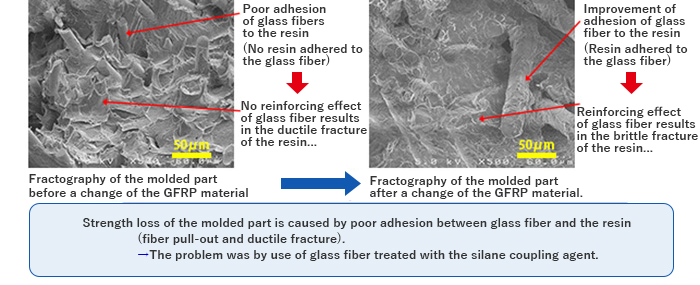
Investigation and analysis of cause of failure of molded rubber parts
- Analysis of the formulation of raw materials in rubber in order to identify the root cause of the degradation
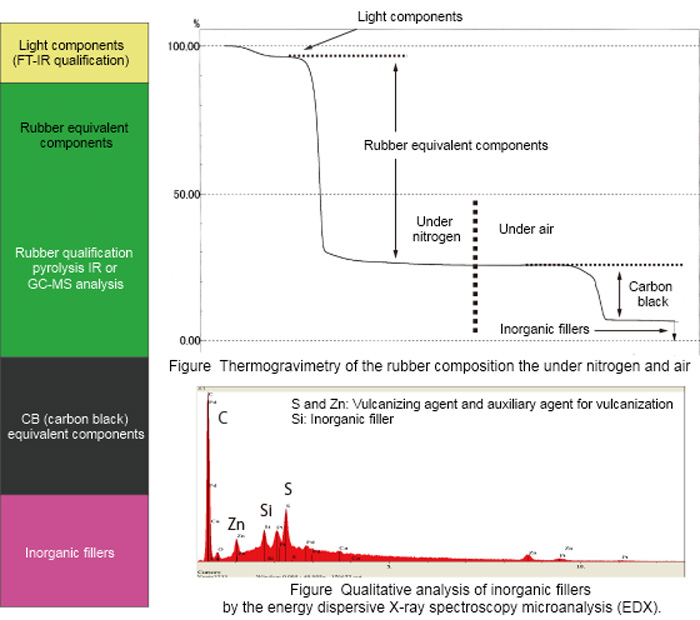
- Morphology of cracks
(1)Ozone cracking starts in the horizontal (stretch) direction and the vertical direction.
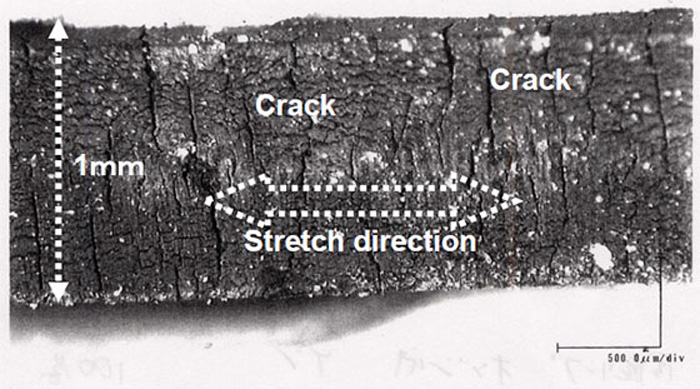
(2) Ozone cracking starts in the horizontal (stretch) direction and the vertical direction.
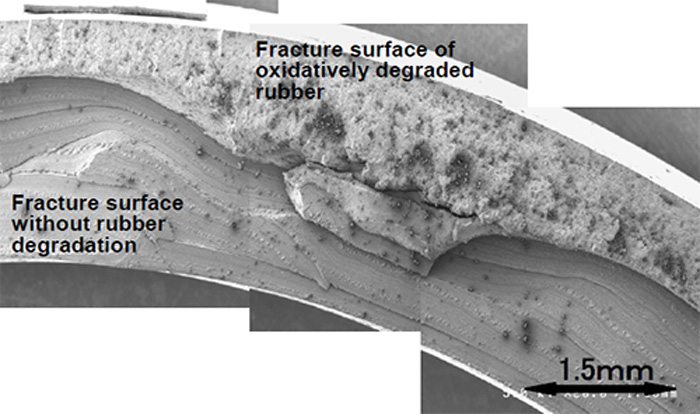