Analysis and Investigation of Electronic Components/Electronic Devices
Mounted Part Defects/Reliability Tests of Solder
Solder joint interface degradation [Failure of mounting portion]
Degradation of the joint interface due to the generation of a large quantity of Kirkendall voids*. Due to the excessive thermal effect at the time of mounting, the thermal effect in the use environment, etc.,
the intermetallic compound layer may grow, and a large quantity of Kirkendall voids may be generated.
*Generally, Kirkendall voids are generated by accumulation of atomic holes (lattice defects) formed by imbalance of mutual diffusion without disappearing. In the case of Sn/Cu interface, it is considered that the amount of Sn diffusion is less than that of Cu diffusion, resulting in accumulation of voids at the interface between the intermetallic compound and the Cu.
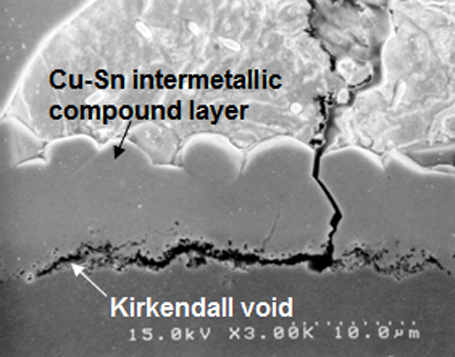
effect of the use environment
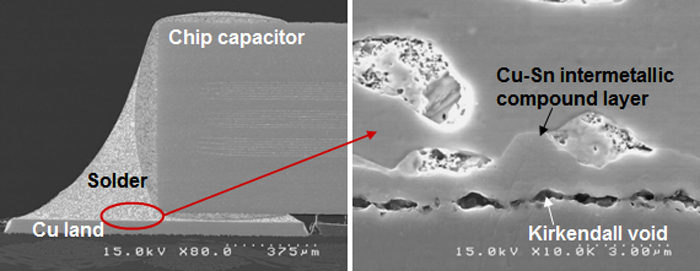
Solder wetting failure [Failure at the mounting portion]
Due to plating failure of electrodes of electronic parts and printed circuit board land, a solder wetting failure occurs.
Below is the case caused by Sn plating failure of the printed circuit board.
At the portion with solder wetting failure, Cu-Sn intermetallic compounds are present on the top surface.
At the Sn/Cu interface, intermetallic compounds are produced. Intermetallic compounds have high melting points and inactive, resulting in degradation in soldering wettability.
It is presumed that the Sn plating of the land is thin in this area and the Cu-Sn intermetallic compounds were exposed to the surface.
In order to check the plating state of the electrodes of electronic part, the solder wettability test may be conducted.
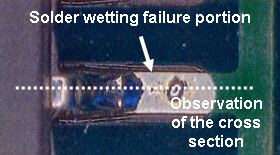
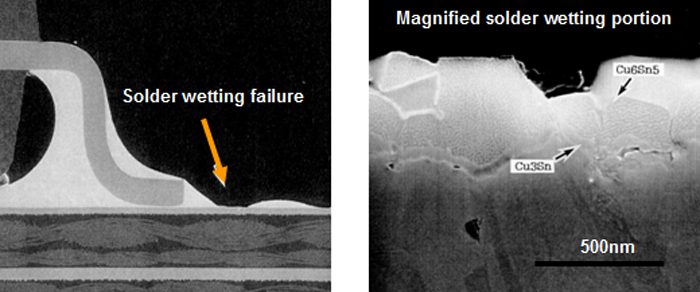
Evaluation of solder joint portion (temperature cycling test) [Reliability test]
As a method for evaluating solder joints of the printed circuit board mounting product, the temperature cycling test is generally used.
In the temperature cycling test, thermal stress (due thermal expansion difference of materials) is loaded to the solder joint, and the change of strength and the crack generating state are examined. Also, the elemental analysis is conducted for examination of the failure portion when necessary.
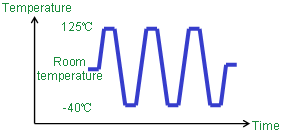
-
Strength variation of solder joint and crack occurrence rate -
Tensile test of QFP terminal -
Shearing test of chip parts
-
Observation of the cross section of solder joint -
EPMA element mapping of void generating portion
(Voids were generated due to the production of Sn-Bi-Pb ternary
eutectic alloy having a melting point of 100ºC or less.)
Migration test of soldering paste flux [Reliability test]
In the soldering paste flux, the activator for removing the oxidation layer on the metal surface is contained. With some kinds of flux, the soldering components are ionized by the effect of flux residues, causing short-circuit between terminals having a potential difference.
As the evaluation method for the flux, the humidity test under DC voltage - the ion migration test in JIS Z3197 "Testing method for soldering fluxes" is defined.
《Testing method》
- Soldering paste is printed on the comb-shaped substrate and solder is applied by reflow.
- The insulation resistance of the comb-shaped substrate is measured (with the application of DC100 V in the 1.0E+14 Ω level)
- The comb-shaped substrate is placed in the constant temperature and humidity chamber (ex., 85ºC-85%RH), DC50 V is applied and the resistance value is monitored.
- After the constant temperature and humidity test is conducted for 1000 hr, the presence or absence of migration and the insulation resistance are checked.
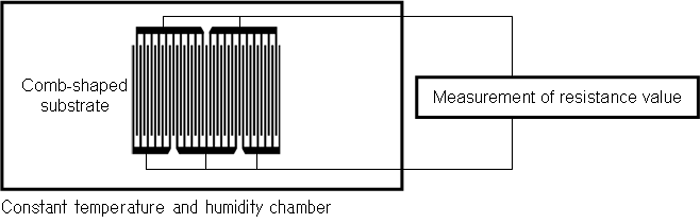
Solder wettability test [Reliability test]
The solder wettability test for electrode of electronic part is defined in JIS Z3198-4 Test methods for lead-free solders-Part 4: Methods for solderbility test by a wetting balance method and a contact angle method. The wetting balance method is described below.
As the evaluation method is influenced by the sample shape, a relative comparison with a (normal) product having the same shape is made.
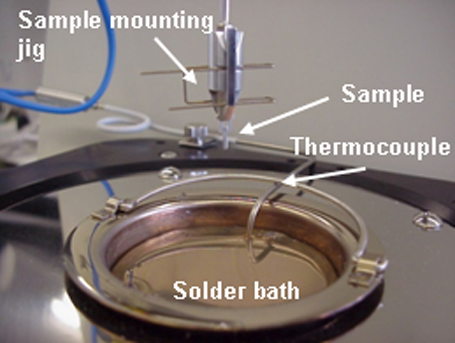
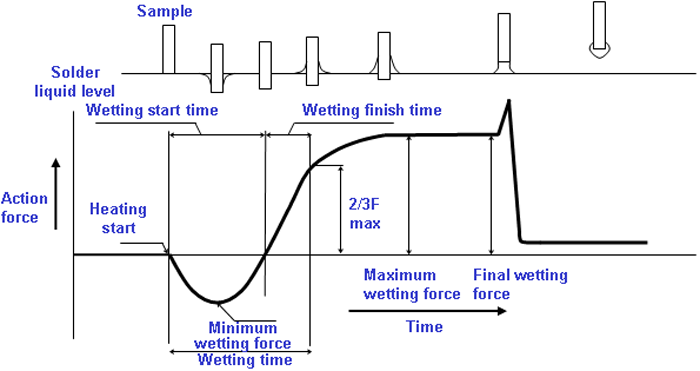
Durability test of solder of mounting substrate (Bending test) [Reliability test]
BGA and CSP are often used in portable devices in which a large stress is applied to the mounting substrate.
One of the durability test for solder joints of BGA or CSP is the evaluation method by the bending test of the mounting substrate (EIAJ ED-4702 Bending test method for substrate, etc.).
The resistance of solder joint is monitored and the number of cycles to rupture is examined.
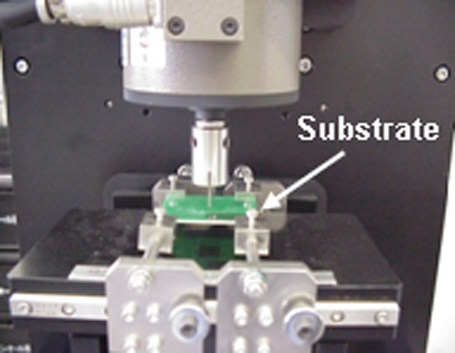
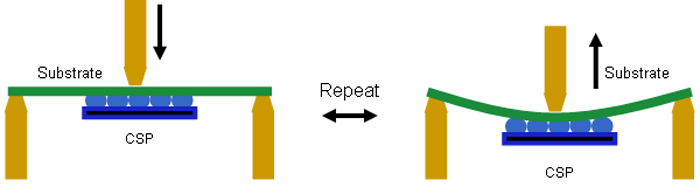
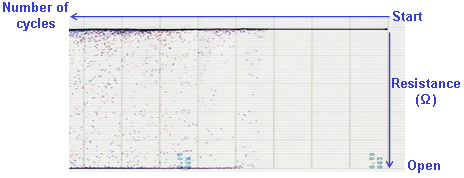